Warehouse Epoxy Flooring Contractors in Greenville, SC
Heavy-Duty Epoxy Floors Designed for Fast-Paced Warehouses
Is your warehouse floor showing signs of wear—cracks, dust, stains, or tire marks? In fast-moving environments like logistics centers and storage facilities, your flooring needs to keep up. You need a system that’s built for strength, safety, and speed.
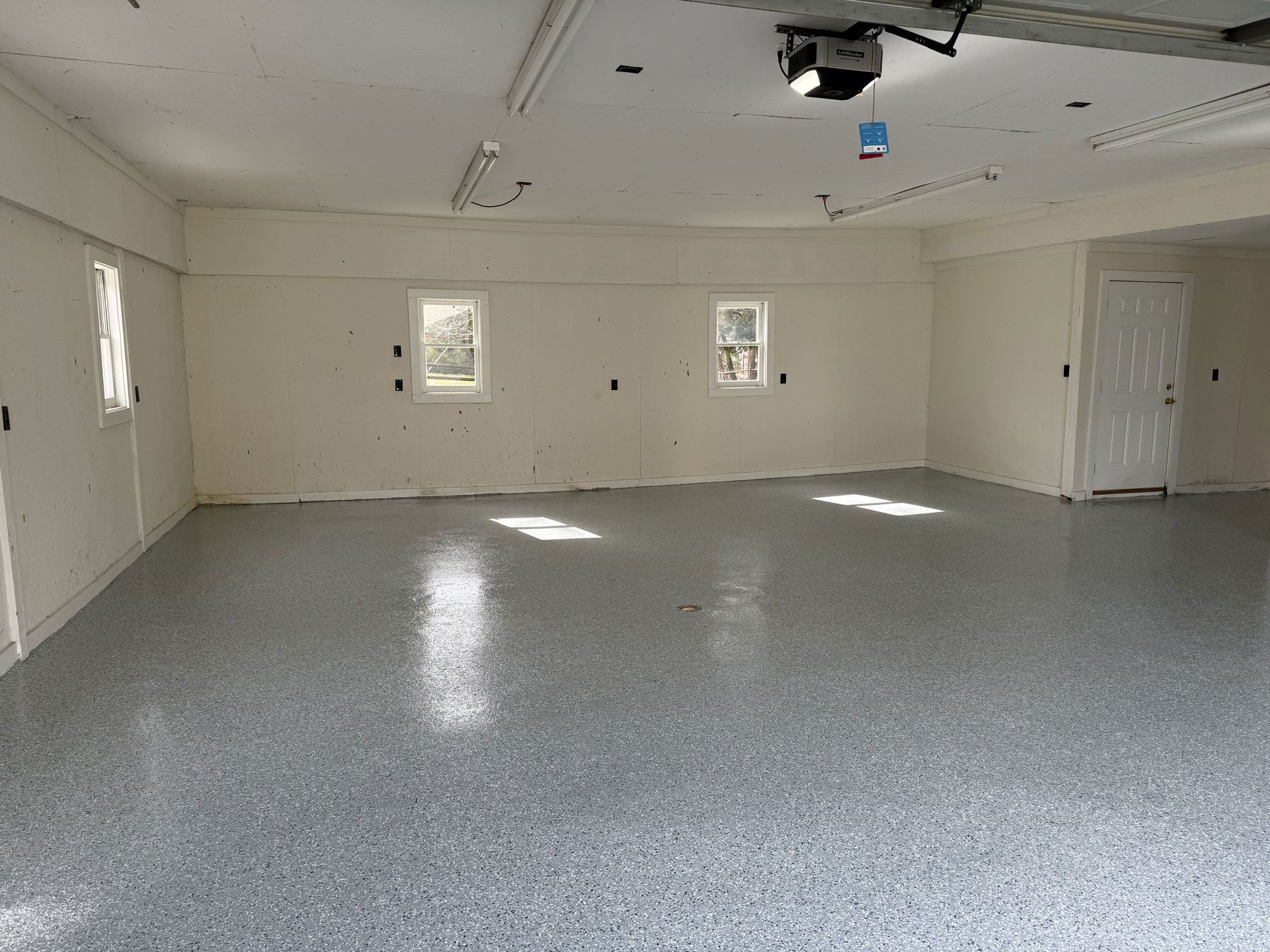
At Greenville Epoxy Flooring Contractors,
we specialize in warehouse epoxy flooring designed for maximum durability and performance. Whether your operation handles heavy machinery, pallet jacks, or constant foot traffic, we create seamless, non-slip floors that stay clean, functional, and tough as nails.

Our epoxy coatings are engineered to resist oil, abrasion, and chemical spills—everything that makes warehouse floors hard to maintain. With professional prep and precision installation, we make sure your floor not only looks good but works hard for years to come.
We proudly serve Greenville, Greer, Simpsonville, Mauldin, and surrounding cities. As a locally owned company, we understand the needs of warehouse operators in the Upstate and tailor every project for real-world performance.
Why Greenville Businesses Choose Our Warehouse Epoxy Floors
In warehouse settings, you can’t afford downtime—or floors that don’t hold up. That’s why we go beyond the basics with in-depth prep, premium materials, and a commitment to delivering floors that meet your facility’s exact needs.
From small storage units to large fulfillment centers, our team has seen it all—and delivered results every time.

Here’s Why We’re a Top Choice in Greenville
We’ve worked on homes across Greenville, Simpsonville, Mauldin, and surrounding neighborhoods. We know the local climate, common concrete issues, and how to apply finishes that hold up to the Upstate’s humidity, rain, and wear.
Proven Experience in Industrial Settings
We’ve installed epoxy flooring in dozens of Upstate warehouses and know how to handle the high demands of industrial traffic, spills, and daily impact.
Heavy Load & Chemical Resistance
Our epoxy coatings are made to resist forklift traffic, dropped tools, fuel spills, and more. They won’t peel, crack, or wear out under pressure.
Expert Prep with Dust-Controlled Equipment
No shortcuts here. We grind and clean the surface using industrial-grade, dust-free equipment and repair imperfections to guarantee lasting adhesion and a smooth finish.
Over a Decade of Local Experience
Minimal Downtime & Fast Installations
We work around your schedule—even nights or weekends if needed. Many warehouse floors are ready to use again in just 2–3 days, minimizing any disruption to operations.
Upfront Quotes, No Surprises
We offer clear, honest pricing from the start. You’ll receive a detailed estimate and job plan so you can prepare your team and schedule with confidence.
Locally Operated & Trusted in Greenville
We live and work right here in the Upstate—and we’re proud to build strong relationships through quality service and dependable results.

What Is Warehouse Epoxy Flooring and Why Is It a Smart Move for Greenville Businesses?
Warehouse epoxy flooring is a commercial-grade resin system applied over concrete to create a smooth, seamless, and highly durable surface that’s built for nonstop use.

It’s designed to handle heavy machinery, rolling loads, foot traffic, and constant wear—making it perfect for:
Fulfillment centers
Logistics hubs
Inventory storage
Equipment rooms
Packaging areas
Loading zones
Shipping docks
No dust clouds. No cracked concrete. Just a tough, low-maintenance floor that supports efficiency and keeps your team moving.
For warehouses in Greenville that demand reliability, safety, and easy maintenance, epoxy flooring checks every box.
Garages
Sunrooms
Why Is Epoxy Flooring the Best Choice for Warehouses in Greenville, SC?
Working with warehouse epoxy flooring contractors in Greenville, SC isn’t just about coating the floor—it’s about investing in durability, safety, and smoother operations.
When your floor works harder, your business runs smoother.
We don’t use cheap kits or cut-rate coatings. Our epoxy systems are industry-leading, high-solids, and made to handle real life—spills, scrapes, moisture, and more. This means you get durable craftsmanship that actually lasts.
Here’s Why Epoxy Is the Preferred Flooring Solution for Busy Warehouse Spaces
Streamlined Maintenance
No need for constant sweeping or industrial cleaners. Epoxy’s non-porous finish keeps dust and dirt under control—saving time and resources.
Resists Chemicals and Impact
Forklifts, oil leaks, dropped boxes—epoxy can take it all. It protects your floor from corrosion, chemicals, and wear without breaking down.
Handles Heavy Traffic with Ease
From pallet jacks to production carts, epoxy stands up to nonstop movement without cracking, flaking, or wearing thin.
Custom Layouts for Efficiency
We can add safety striping, traffic zones, or color-coded areas to help improve workflow, visibility, and OSHA compliance.
Seals and Strengthens Concrete
Epoxy strengthens your existing floor while preventing moisture intrusion, surface damage, and dusting from old concrete.
Enhances Safety and Lighting
Anti-slip options reduce accidents, and the glossy finish reflects light—helping brighten large warehouse interiors without extra fixtures.
Boosts Professional Appearance
Whether clients tour your facility or employees work on-site daily, epoxy flooring adds a polished, organized feel that reflects your standards.
What Type of Epoxy Coating Works Best for Warehouse Floors?
Warehouses have specific needs when it comes to flooring—durability, cleanliness, and safety are non-negotiable. In Greenville’s growing industrial and logistics sectors, epoxy is the preferred choice for warehouse owners who want reliable, low-maintenance floors that support fast-paced operations.
Here are the top epoxy flooring systems suited for warehouse environments:
Solid Color Epoxy: This option is ideal for high-traffic areas like aisles, loading zones, and inventory rows. It provides a clean, uniform appearance while standing up to forklift wheels, pallet jacks, and heavy carts. Facilities across Greenville and surrounding areas rely on this finish for its strength and easy maintenance.
Flake Epoxy Systems: While not as common in the heaviest-use zones, flake epoxy is great for warehouse offices, break rooms, and reception areas. The decorative flakes help reduce visible dirt, improve slip resistance, and add a more finished look. Many warehouse managers in Mauldin and Simpsonville use flake systems to upgrade their non-operational spaces.
Line-Striped or Zoned Epoxy: This system includes solid epoxy with integrated safety markings or color-coded zones for improved traffic flow and OSHA compliance. Popular in larger operations, especially around Taylors and Fountain Inn, these layouts make it easier to navigate the floor safely and efficiently.
Need Help Selecting the Right Option?
Our warehouse epoxy contractors in Greenville will walk your facility, discuss your needs, and help you decide on a system that performs well under pressure.
What’s Our Process for Installing Epoxy in Greenville Warehouses?
We understand that warehouse downtime costs money. That’s why we offer fast, efficient installation without compromising quality. Whether we’re working after hours or in phases, our process is built to minimize disruption and maximize long-term value.
Extremely Durable
Here’s How We Install Warehouse Epoxy Flooring
Site Walkthrough & Estimate
We assess square footage, traffic zones, current flooring condition, and layout, then build a custom quote for your operation.
Surface Grinding & Crack Repair
Our industrial grinders remove old coatings, dirt, and surface damage. We also repair joints and patch spalls to ensure a smooth surface.
Moisture Barrier Primer
Essential for large concrete slabs, especially in Greenville’s humid environment. This primer helps prevent vapor intrusion and bond failure.
Base Coat Application
We apply a high-solids epoxy layer designed to resist abrasion, impact, and chemical spills.
Optional Markings or Flakes
Add directional striping, flake texture, or color zoning to improve safety and organization.
Protective Topcoat
A tough sealer finishes the job, protecting your investment from tire wear, oil leaks, and daily operations.
Cure Time & Return to Service
Light foot traffic in 24 hours, heavy equipment in 48–72 hours, depending on product and temperature.
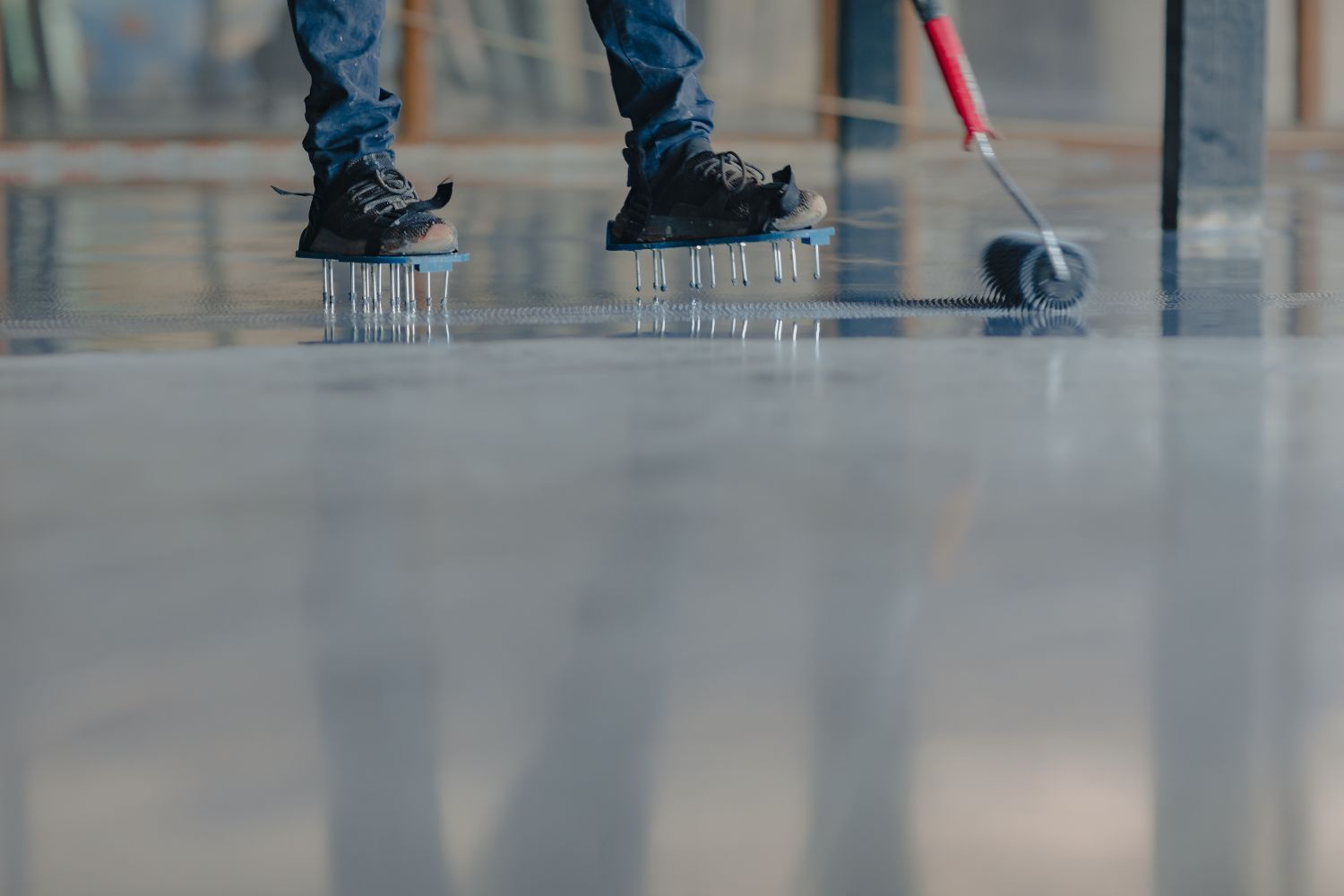
How Much Does Warehouse Epoxy Flooring Cost in Greenville, SC?
Managing a warehouse means keeping things efficient—and that starts from the ground up. If you're considering epoxy flooring for your warehouse in Greenville, SC, we know you need real numbers, not rough estimates.
On average,
warehouse epoxy flooring costs between $4.50 and $9 per square foot. The final price depends on floor size, prep work, finish type, and how tough the system needs to be. Heavy equipment or safety striping may increase the cost slightly.
Here’s a helpful starting point to understand your investment:
Floor Size | Solid Epoxy Finish | Flake or Quartz | Safety Zones/Striping |
---|---|---|---|
1,500 sq ft | $6,000–$10,500 | $7,200–$11,500 | Add $1.00–$2.00/sq ft |
3,000 sq ft | $12,000–$19,000 | $14,500–$21,500 | Add $1.00–$2.00/sq ft |
5,000+ sq ft | Custom Quote | Custom Quote | Custom Quote |
All pricing includes concrete prep, coatings, labor, and standard topcoat. We’ll visit your facility to evaluate surface conditions and layout before giving you a firm quote.
What Impacts the Cost of Warehouse Epoxy Floors?
Every facility has its own wear-and-tear, and a few key variables can affect pricing:
Current floor condition – Old coatings, cracks, or oil contamination require more surface prep, grinding, or patching.
Coating type – Solid color is most economical. Flake, quartz, or chemical-resistant finishes cost more due to material and labor.
Layout and workflow – Columns, narrow paths, drains, or high-traffic intersections take longer to complete.
Add-ons – Striping for safety zones, forklift lanes, or walkways may increase cost slightly but improve functionality.
Downtime and scheduling – We offer phased installations or off-hours to minimize business disruption.
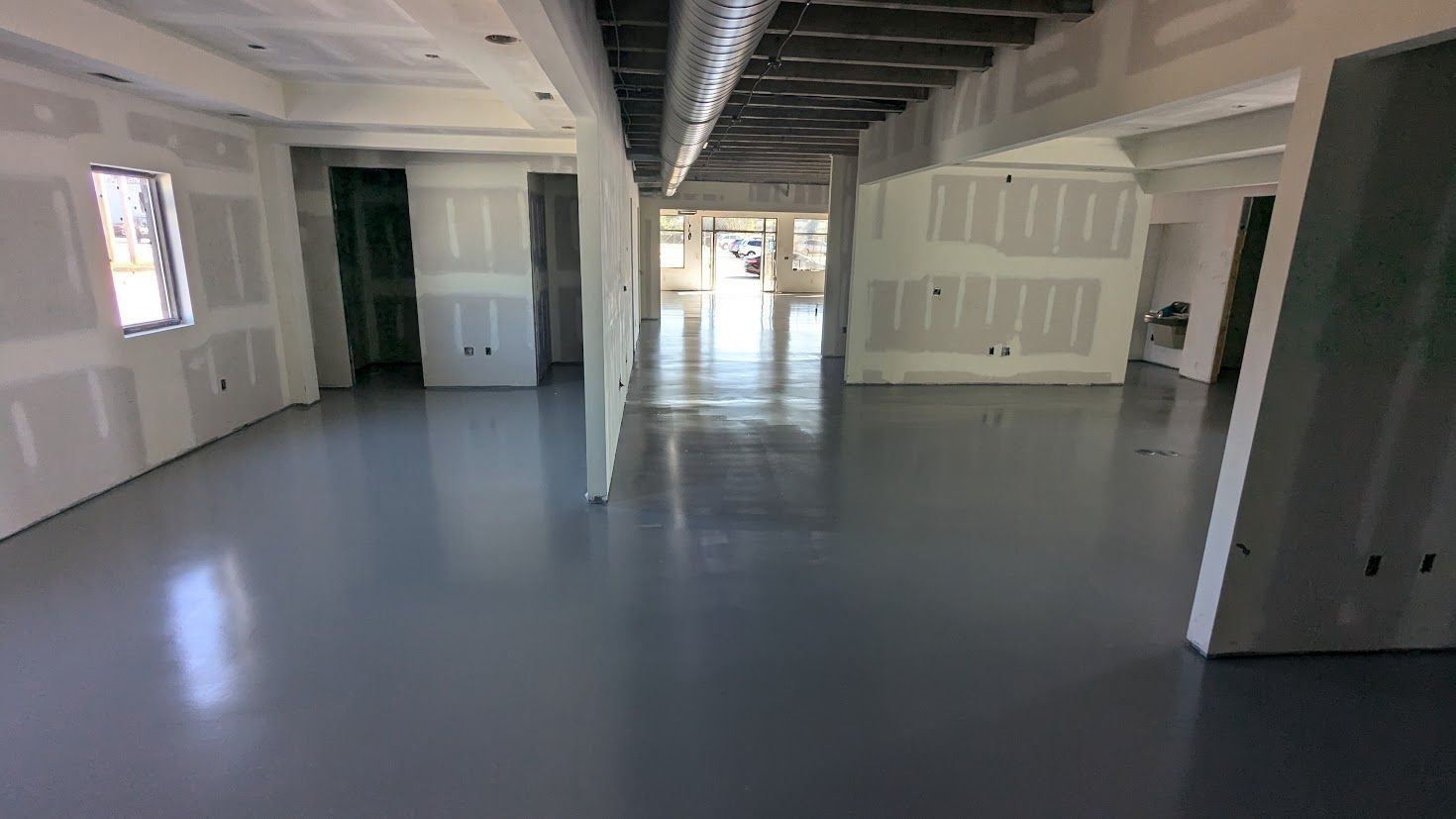
Do You Install Warehouse Epoxy Floors Near Me?
Yes! We provide warehouse epoxy flooring throughout Greenville and nearby areas, including:
Simpsonville
Mauldin
Greer
Travelers Rest
Taylors
Fountain Inn
Easley
Anderson
Powdersville
Berea
FAQs About Warehouse Epoxy Flooring – Greenville Edition
Can epoxy handle forklifts and heavy racking?
Yes. We use industrial-grade systems designed for high-load and rolling equipment.
How long does installation take?
Most warehouse floors are completed in 2–4 days. Larger jobs may require phased work to keep your team moving.
Is it slippery when wet?
We offer slip-resistant textures and finishes to improve traction and safety in all conditions.
Can I customize safety striping or zones?
Absolutely! We can integrate forklift lanes, walking paths, or hazard areas directly into the coating.
Do you offer a warranty?
Yes. We include a 5-year workmanship warranty on all warehouse epoxy flooring systems.
Make Your Warehouse Floor Work Smarter
Our epoxy flooring solutions help Greenville warehouse owners reduce maintenance, improve safety, and support smooth operations. We’ll build a floor that keeps up with your day-to-day demands.
Call (864) 252-1101
Request a Free Estimate
Let’s create a safer, stronger, and better-looking floor—without the downtime.